WELDING
Welding may be a fabrication process that joins materials, usually metals or thermoplastics, by using high heat to melt the parts together and allowing them to chill, causing fusion. Welding is distinct from lower temperature metal-joining techniques like brazing and soldering, which don't melt the bottom metal.
In addition to melting the bottom metal, a filler material is usually added to the joint to make a pool of molten material (the weld pool) that cools to make a joint that, supported weld configuration (butt, full penetration, fillet, etc.), are often stronger than the bottom material (parent metal). Pressure can also be utilized in conjunction with heat or by itself to supply a weld. Welding also requires a sort of shield to guard the filler metals or melted metals against being contaminated or oxidized.
METHODS IN WELDING
1.Shielded Metal Arc Welding
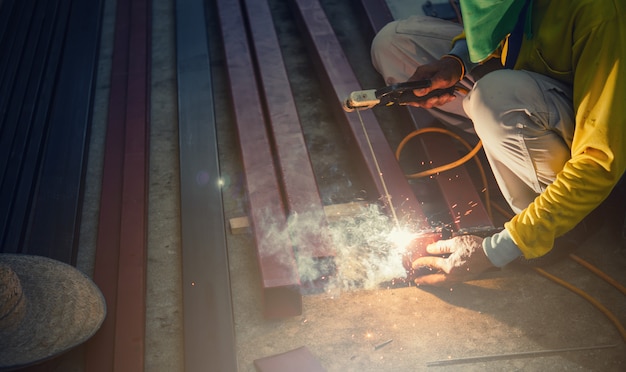
Shielded metal arc welding (SMAW), also referred to as manual metal arc welding (MMA or MMAW), flux shielded arc welding or informally as stick welding may be a manual arc welding process that uses a consumable electrode covered with a flux to get the weld.
An electric current, within the sort of either AC or DC from a welding power supply, is employed to make an electrical arc between the electrode and therefore the metals to be joined. The workpiece and therefore the electrode melts forming a pool of molten metal (the weld pool) that cools to make a joint. because the weld is laid, the flux coating of the electrode disintegrates, giving off vapours that function a shielding gas and providing a layer of slag, both of which protect the weld area from atmospheric contamination.
Because of the flexibility of the method and therefore the simplicity of its equipment and operation, shielded metal arc welding is one among the world's first and hottest welding processes. It dominates other welding processes within the maintenance and repair industry, and though flux-cored arc welding is growing in popularity, SMAW continues to be used extensively within the construction of heavy steel structures and in industrial fabrication. the method is employed primarily to weld iron and steels (including stainless steel) but aluminium, nickel and copper alloys also can be welded with this method.
2.GAS TUNGSTEN ARC WELDING
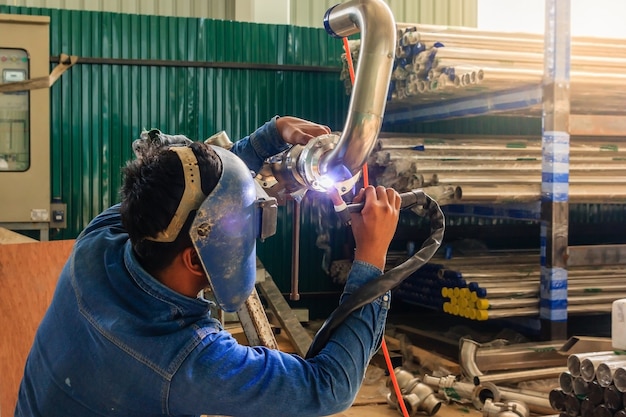
Gas tungsten arc welding (GTAW), also referred to as tungsten noble gas (TIG) welding, is an arc welding process that uses a non-consumable tungsten electrode to supply the weld. The weld area and electrode are shielded from oxidation or other atmospheric contamination by an inert shielding gas (argon or helium), and a filler metal is generally used, though some welds, referred to as autogenous welds, don't require it. When helium is employed, this is often referred to as heliarc welding. A constant-current welding power supply produces electricity, which is conducted across the arc through a column of highly ionized gas and metal vapours referred to as a plasma.
GTAW is most ordinarily won't to weld thin sections of chrome steel and non-ferrous metals like aluminium, magnesium, and copper alloys. the method grants the operator greater control over the weld than competing processes like shielded metal arc welding and gas metal arc welding, allowing stronger, higher quality welds. However, GTAW is relatively more complex and difficult to master, and furthermore, it's significantly slower than most other welding techniques. A related process, plasma arc welding, uses a rather different welding torch to make a more focused welding arc and as a result, 's often automated.
3.GAS METAL ARC WELDING

Gas metal arc welding (GMAW), sometimes mentioned by its subtypes metal noble gas (MIG) welding or metal active gas (MAG) welding, maybe a welding process during which an electrical arc forms between a consumable MIG wire electrode and therefore the workpiece metal(s), which heats the workpiece metal(s), causing them to melt and join. alongside the wire electrode, a shielding gas feeds through the welding gun, which shields the method from atmospheric contamination.
The process is often semi-automatic or automatic. a continuing voltage, the DC power source is most ordinarily used with GMAW, but constant current systems, also as AC, are often used. There are four primary methods of metal transfer in GMAW, called globular, short-circuiting, spray, and pulsed-spray, each of which has distinct properties and corresponding advantages and limitations.
Originally developed within the 1940s for welding aluminium and other non-ferrous materials, GMAW was soon applied to steels because it provided faster welding time compared to other welding processes. the value of noble gas limited its use in steels until several years later when the utilization of semi-inert gases like CO2 became common. Further developments during the 1950s and 1960s gave the method more versatility and as a result, it became a highly used process. Today, GMAW is that the commonest industrial welding process, preferred for its versatility, speed and therefore the relative simple adapting the method to robotic automation. Unlike welding processes that don't employ a shielding gas, like shielded metal arc welding, it's rarely used outdoors or in other areas of moving air. A related process, flux-cored arc welding, often doesn't use a shielding gas, but instead employs an electrode wire that's hollow and crammed with flux.
4.FLUX-CORED ARC WELDING
![Flux cored arc welding process [5] | Download Scientific Diagram](https://www.researchgate.net/profile/Pavel_Layus/publication/280575269/figure/fig5/AS:284505551196161@1444842817502/Flux-cored-arc-welding-process-5.png)
Flux-cored arc welding (FCAW or FCA) may be a semi-automatic or automatic arc welding process. FCAW requires a continuously-fed consumable tubular electrode containing a flux and a constant-voltage or, less commonly, a constant-current welding power supply. An externally supplied shielding gas is usually used, but often the flux itself is relied upon to get the required protection from the atmosphere, producing both gaseous protection and liquid slag protecting the weld. the method is widely utilized in construction due to its high welding speed and portability.
FCAW was first developed within the early 1950s as an alternate to shielded metal arc welding (SMAW). The advantage of FCAW over SMAW is that the utilization of the stick electrodes utilized in SMAW makes no sense. This helped FCAW to beat many of the restrictions related to SMAW.
5.SUBMERGED ARC WELDING

Submerged arc welding (SAW) may be a common arc welding process. the primary patent on the submerged-arc welding (SAW) process was taken a call at 1935 and covered an electrical arc beneath a bed of granulated flux. Originally developed and patented by Jones, Kennedy and Rothermund, the method requires a continuously fed consumable solid or tubular (metal cored) electrode. The molten weld and therefore the arc zone are shielded from atmospheric contamination by being "submerged" under a blanket of granular fusible flux consisting of lime, silica, manganese oxide, calcium fluoride, and other compounds. When molten, the flux becomes conductive and provides a current path between the electrode and therefore the work. This thick layer of flux completely covers the molten metal thus preventing spatter and sparks also as suppressing the extreme ultraviolet and fumes that are a neighbourhood of the shielded metal arc welding (SMAW) process.
SAW is generally operated within the automatic or mechanized mode, however, semi-automatic (hand-held) SAW guns with pressurized or gravity flux feed delivery are available. the method is generally limited to the flat or horizontal-fillet welding positions (although horizontal groove position welds are through with a special arrangement to support the flux). Deposition rates approaching 45 kg/h (100 lb/h) are reported — this compares to ~5 kg/h (10 lb/h) (max) for shielded metal arc welding. Although currents starting from 300 to 2000 A are commonly utilized, currents of up to 5000 A have also been used (multiple arcs).
Single or multiple (2 to 5) electrode wire variations of the method exist. SAW strip-cladding utilizes a flat strip electrode (e.g. 60 mm wide x 0.5 mm thick). DC or AC power is often used, and combinations of DC and AC are common on multiple electrode systems. Constant voltage welding power supplies are most ordinarily used; however, constant current systems together with a voltage sensing wire-feeder are available.
6.ELECTRO SLAG WELDING
Electroslag welding (ESW) may be a highly productive, single-pass welding process for thick (greater than 25 mm up to about 300 mm) materials during a vertical or on the brink of a vertical position. (ESW) is analogous to electron gas welding, but the most difference is that the arc starts during a different location. an electrical arc is initially struck by a wire that's fed into the specified weld location then flux is added. Additional flux is added until the molten slag, reaching the tip of the electrode, extinguishes the arc. The wire is then continuously fed through a consumable guide tube (can oscillate if desired) into the surfaces of the metal workpieces and therefore the filler metal is then melted using the electric resistance of the molten slag to cause coalescence. The wire and tube then move up along the workpiece while a copper retaining shoe that was put into place before starting (can be water-cooled if desired) is employed to stay the weld between the plates that are being welded. Electroslag welding is employed mainly to hitch low steel plates and/or sections that are very thick. It also can be used on steel if certain precautions are observed and for giant cross-section aluminium busbars.[1] This process uses an immediate current (DC) voltage usually starting from about 600 A and 40-50 V, higher currents are needed for thicker materials. Because the arc is extinguished, this is often not an arc process.
GLASS WELDING, PLASTIC WELDING AND LASER WELDING
GLASS WELDING
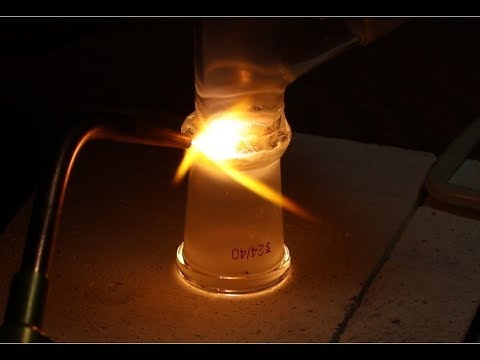
Glass welding may be a common practice during glassblowing. it's used fairly often within the construction of lighting, neon signs, flash tubes, scientific equipment, and therefore the manufacture of dishes and other glassware. it's also used during glass casting for joining the halves of glass moulds, making items like bottles and jars. Welding glass is accomplished by heating the glass through the glass transition, turning it into a thick, formable, liquid mass. Heating is typically through with a gas or oxy-gas torch, or a furnace because the temperatures for melting glass are often quite high. This temperature may vary, counting on the sort of glass. for instance, glass becomes a weldable liquid at around 1,600 °F (870 °C), and maybe welded with an easy propane torch. On the opposite hand, quartz (fused silica) must be heated to over 3,000 °F (1,650 °C), but quickly loses its viscosity and formability if overheated, so an oxyhydrogen torch must be used. Because glass is extremely brittle in its solid-state, it's often susceptible to cracking upon heating and cooling, especially if the heating and cooling are uneven. this is often because the brittleness of glass doesn't leave uneven thermal expansion. Glass that has been welded will usually be got to be cooled very slowly and evenly through the glass transition, during a process called annealing, to alleviate any internal stresses created by a gradient.
There are many sorts of glass, and it's commonest to weld using an equivalent type. Different glasses often have different rates of thermal expansion, which may cause them to crack upon cooling once they contract differently. as an example, quartz features a very low thermal expansion, while soda-lime glass features a very high thermal expansion. When welding different glasses to every other, it's usually important to closely match their coefficients of thermal expansion, to make sure that cracking doesn't occur. Also, some glasses will simply not mix with others, so welding between certain types might not be possible.
Glass also can be welded to metals and ceramics, although with metals the method is typically more adhesion to the surface of the metal instead of commingling of the 2 materials. However, certain glasses will typically bond only to certain metals. for instance, glass bonds readily to copper or molybdenum, but to not aluminium. Tungsten electrodes are often utilized in lighting but won't bond to quartz, therefore the tungsten is usually wetted with molten borosilicate glass, which bonds to both tungsten and quartz. However, care must be taken to make sure that each one material have similar coefficients of thermal expansion to stop cracking both when the thing cools and when it's heated again. Special alloys are often used for this purpose, ensuring that the coefficients of expansion match, and sometimes thin, metallic coatings could also be applied to a metal to make an honest bond with the glass.
PLASTIC WELDING

Plastic welding is welding for semi-finished plastic materials and is described in ISO 472 as a process of uniting softened surfaces of materials, generally with the assistance of heat (except solvent welding). Welding of thermoplastics is accomplished in three sequential stages, namely surface preparation, application of heat and pressure, and cooling. Numerous welding methods are developed for the joining of semi-finished plastic materials. supported the mechanism of heat generation at the welding interface, welding methods for thermoplastics are often classified as external and internal heating methods.
LASER WELDING
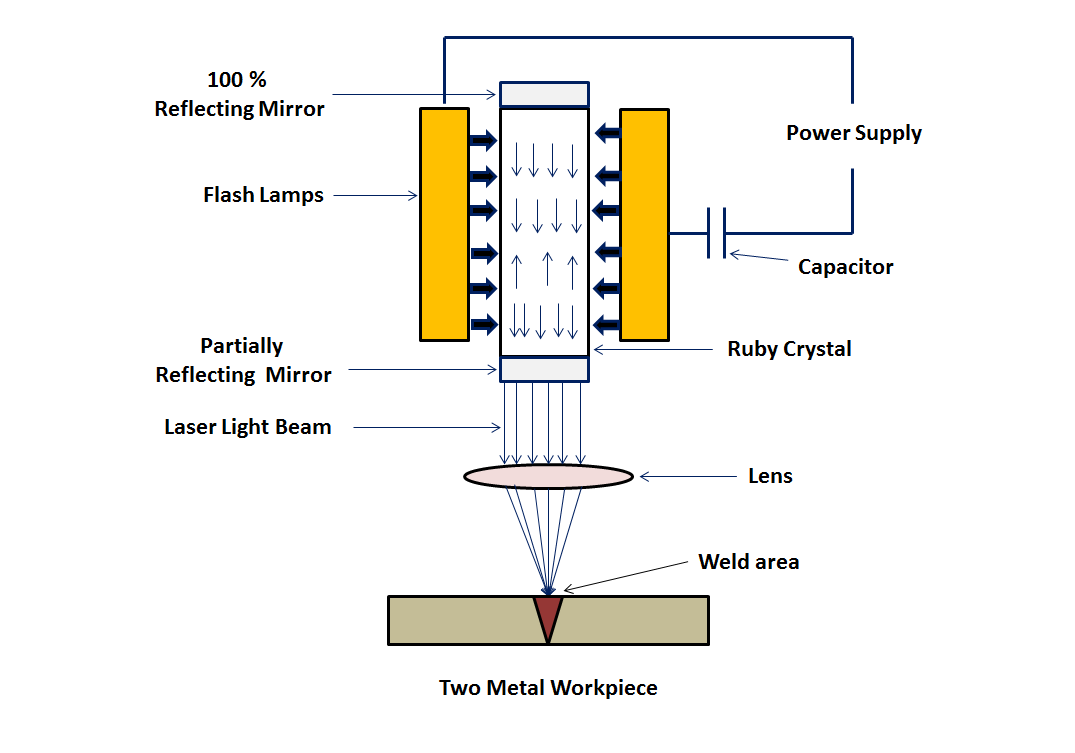
Laser beam welding (LBW) may be a welding technique wont to join pieces of metal or thermoplastics through the utilization of a laser. The beam provides a concentrated heat source, allowing narrow, deep welds and high welding rates. the method is usually utilized in high volume applications using automation, as within the automotive industry. it's supported keyhole or penetration mode welding.
No comments:
Post a Comment