DEFINITION
Cast irons are basically alloys of iron and carbon-like steels during which forged iron the carbon percentage varies between 2.0% to 6.67%. The solubility limit of carbon is going to be quite that in austenite and fewer than the content of cementite. High carbon percentage makes cast-iron makes very brittle (hard).
Therefore, most commercially manufactured forged iron has 2.5% to 4% carbon.
forged iron can't be rolled, drawn or worked at a temperature as forged iron has very low ductility and poor malleability. But, castiron is often readily melted and cast into complicated shapes. It is often machined to the ultimate dimensions if needed. the sole suitable process applied to those alloys is casting. Hence the name was given cast irons. The melting temperature of forged iron is within the range of 1150℃ -1250℃ which is a smaller amount in comparison to the melting of steels is within the range of 1350℃-1500℃ hence it's easy to melt. Cast irons have good corrosion resistance and fewer shrinkage during solidification. Hence castiron is often used over a good and useful range the properties are easily adjusted.
CLASSIFICATION OF CAST IRONS
Castiron are classified based on the following criteria
1. According to the furnace used
- cupola cast irons
- air furnace cast irons
- electric furnace cast irons
- duplex cast irons
- low carbon, low silicate cast irons
- high carbon, low sulphur cast irons
- nickel alloy cast irons, etc
- white cast iron
- malleable cast iron
- grey cast iron
- nodular cast iron
- mottled cast iron
- chilled cast iron
- alloy cast iron

The fact that its freshly broken surface shows a bright white fracture gives its name as white cast iron.
White cast iron has all most all its carbon chemically bonded with the iron as iron carbide. Iron carbide is very hard and brittle. Thus, white cast iron possesses excellent abrasive wear resistance under normal conditions and it is brittle, not machinable in nature. Cast iron may be solidified by using fairly low silicon content, this can be in sand moulds.
2.malleable cast iron
Malleable cast iron can be rolled can be hammered and rolled to different shapes. A controlled conversion process of white cast iron, malleable cast iron is obtained .an alloy, malleable cast iron contains contains contains chromium and Nickle hence, they have high strength and are corrosion resistant. Malleable cast iron process high yield strength, high youngs modules, low coefficient of thermal expansion, good wear resistance and good vibration damping capacity
3. Grey cast iron

Grey cast iron is basically an alloy of carbon and silicon with iron. It is readily cast into a sand mould to get a required shape. It is marked by the presence of graphite flakes in a matrix of ferrite, pearlite or austenite. The metal volume of 10% is occupied by the graphite flakes. Length of flakes may vary from 0.005 mm, grey cast iron melting a low melting possesses good machinability, high resistance to wear and also high vibration damping capacity. Grey cast iron has an excellent casting quality for the production of simple and complex shapes.
4.Nodular cast iron
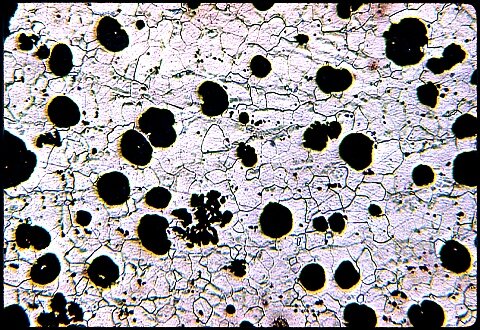
Nodular cast iron is also known as the ductile iron. Unlike the long flakes in the grey cast iron, graphics appear as rounded particles on nodules in cast iron. The periodizing elements when added to melt estimate sulphur and oxygen, which change the solidification characteristics and possibly account for nodulizing. The properties of ductile cast iron depend upon the metal composition and the cooling rate. It possesses good castability and excellent wear resistance .the damping capacity is intermediate between that of that cast iron and steel. Nodular cast iron is mostly used in internal combustion engines.
5.Mottled cast iron
Mottled forged iron is widely used for mill rolls thanks to its content of both lede barite and graphite within the microstructure. ... Increase of cooling rate within this range resulted within the increase of transformed lede buried content and reduce of graphite content in the microstructure of forged iron.
6.Chilled cast iron
Chilled cast iron is a combination of a grey cast iron and white cast iron. White cast iron is observed at the surface of the cast, while grey cast iron is a central core. It can be produced by carefully controlling the composition of alloy and rate of cooling. The normal rate of cooling at the surface produces white cast iron and a slower rate of cooling results in a grey structure at the centre. This type of cast iron is as produced to meet the properties of white cast iron as well as grey cast iron. The surface of chilled cast iron (or chilled cast iron)decreases within an increase in the content of carbon, silicon and graphitizing element. Carbon and silicon composition in chilled cast iron is
carbon → 2-2.5%
silicon→3-3.5%
Applications
- railway freight car wheels
- grinding balls
- sprockets
- road rollers.
- ploughshares
- crushing rolls
- hammers die, stamps shoes etc.

Alloy cast irons are considered to be those casting alloys supported the iron-carbon-silicon system that contains one or more alloying elements intentionally added to reinforce one or more useful properties. Alloy cast irons are often classified as white cast irons, corrosion-resistant cast irons, and heat-resistant cast irons. this text discusses abrasion-resistant chilled and white irons, high-alloy corrosion-resistant irons, and medium-alloy and high-alloy heat-resistant grey and ductile irons. The article outlines during a list the approximate ranges of alloy content for various sorts of alloy cast irons. The article explains the consequences of alloying elements and therefore the effects of inoculants. In most cast irons, it's the interaction among alloying elements that has the best effect on properties. Inoculants aside from appropriate graphitizing or modularizing agents are used rarely, if ever, in high-alloy corrosion-resistant or heat-resistant irons.
CHARACTERISTICS OF CAST IRONS OVER STEELS
- Cast irons are inexpensive among all the commercial alloys. The raw materials used for the manufacturing of cast iron are of least expensive, which involve pig iron, cast iron scrap, steel scrap, ferrosilicon, high silicon pig iron, iron ore, limestone, coke etc.
- The melting temperature of cast iron is low range from (1150℃-1250℃)in comparison to steel, which ranges from (1350℃-1500℃). Hence cast irons can be melted easily.
- Cast irons can be cast easily, due to their high fluidity of melt and low shrinkage while solidification.
- Cast irons in comparison to steels can be adjusted easily to a large extent and useful range.this is possible by applying appropriate alloying. better foundry control and suitable heat treatment process to them.
- Generally, cast irons are brittle in nature and have low mechanical properties in contrast to steels.
No comments:
Post a Comment