DEFINITION
making scaled 3-dimensional physical objects directly from 3D-CAD data without
using part-depending tools. it had been originally called “3D Printing” and remains frequently
called that. Together with the well established “Subtractive Manufacturing”, like milling or
turning, and therefore the “Formative Manufacturing”, like casting or forging, Additive
Manufacturing provides the third supporting pillar of the whole manufacturing technology /Bur93/.
- Additive Manufacturing (AM)
- Additive Layer Manufacturing (ALM)
- Additive Digital Manufacturing (DM)
- Layer Based Manufacturing(LBM)
- Layer Oriented Manufacturing(LOM)
- Layer Manufacturing(LM)
- Rapid Technology(RT)
- Rapid Prototyping, (RP)
- Rapid Tooling(RT)
- Rapid Manufacturing(RM)
- Digital Fabrication(DF)
- Digital Mock-Up(DM)
- Direct Manufacturing(DM)
- , Direct Tooling(DT)
- 3D Printing
- 3D Modeling
principle
TYPES OF 3D-PRINTING
- stereolithography (SLA)
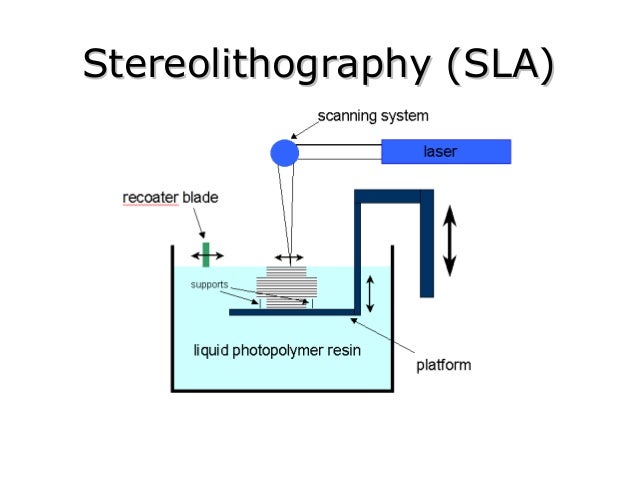
- selective laser sintering (SLS)
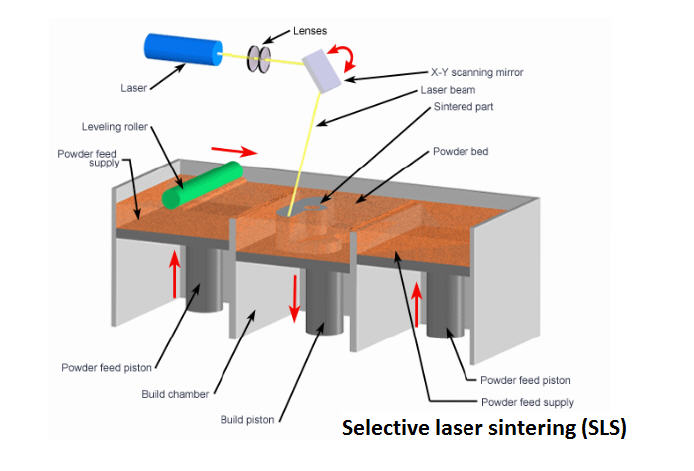
- fused deposition modelling (FDM)

- digital light process (DLP)

- multi-jet fusion(MJF)

- poly jet
- direct metal laser sintering (DMLS)

- electron beam melting (EBM)

SOME OF THE MATERIALS USED IN ADDITIVE MANUFACTURING
Distinct Characteristics:
- nylon know for its durability
- It has an excellent strength to flexibility ratio.
- Nylon has very little warpage.
- This type of material can be easily dyed or coloured.
Disadvantages:
- Since nylon is hygroscopic, it should be kept dry.
- It has a shelf life of 12 months.
- This material can shrink during cooling, thus, prints may be less precise.
- Printer suitability also varies.
2.ABS
- It is one of the foremost accessible and cheap materials for 3D printing.
- ABS is very available and features a big variety of colours.
- This material features a longer lifespan compared to Nylon.
- It is also mechanically strong.
- This material isn't suitable for hobbyists. it's only used for manufacturers and engineers who are trying to find high-quality prototype production.
- It requires a heated bed when printing.
- Since ABS materials have a high freezing point
- it's a bent to experience warping if cooled while printing.
- This type of filament may be a non-biodegradable toxic material that releases toxic fumes with awful smell at heat.
3.RESIN
Resin is one of the most used material in 3D printing. It is mainly used in technologies such as SLA, DLP, Multijet or CLIP technologies. Various types of resins can be used in 3D printing such as castable resins, tough resins, flexible resins, etc.
Distinct characteristics:
- It can be used in many applications.
- It has low shrinkage.
- Resin materials have high chemical resistance.
- This material is rigid and delicate.
Disadvantages:
- It is expensive.
- This type of filament also expires.
- It needs to be stored securely due to its high photo-reactivity.
- When exposed to heat, it can cause premature polymer
4.PLA(POLYLACTIC ACID)
PLA or Polylactic Acid are made from renewable resources such as sugarcane or cornstarch. It is also called “green plastic”. It is mostly used in primary and secondary schools since it is safe to use and easy to print with. It is also used in FDM desktop printing.
Distinct characteristics:
- PLA is easy to print since it has low warping.
- It can also be printed on a cold surface.
- It can print with sharper corners and features compared to ABS material.
- This material is available in different colours.
Disadvantages:
- PLA materials are not very sturdy and can deform when exposed to extreme heat.
- This type of material is less sturdy.
5.GOLD AND SILVER
Today, it is possible to 3D print using gold and silver. These filaments are sturdy materials and are processed in powder form. These materials are generally used in the jewellery sector. These metal use the DMLS (Direct Metal Laser Sintering) or SLM process for printing.
Distinct Characteristics:
- It has high electrical conductance.
- It is heatproof.
Disadvantages:
- Printing with gold and silver are expensive.
- It takes a lot of effort and time to get it right.
- Both gold and silver are difficult to work with lasers because of its high reflectivity and high thermal conductivity.
- Since extremely high temperature is needed to print these materials, a regular FDM 3D printer is not suitable to use.
6.STAINLESS STELL
Stainless steel is printed by fusion or laser sintering. Two possible technologies can be used for this material. It can be DMLS or SLM technologies. Since stainless steel is all about strength and detail, it is perfect to use for miniatures, bolts and key chains
Distinct Characteristics:
- Stainless steel can be heat treated to improve strength and hardness.
- It performs well in high strength applications.
- It provides strong resistance against corrosion.
- It has a high ductility.
Disadvantages:
- Building time for 3D printing using these metals is much longer.
- Printing with stainless steel is expensive.
- Printing size is limited.
7.TITANIUM
Titanium is the strongest and lightest material for 3D printing. It is used in the process called Direct Metal Laser Sintering. This metal is mainly used in high-tech fields such as space exploration, aeronautics and medical field.
Distinct Characteristics:
- It provides greater complexity and resolution in design.
- It offers industrial designers precision in design.
- It has an average surface roughness.
- Titanium is also biocompatible and resists corrosion.
Disadvantages:
- Titanium 3D printing is expensive.
8.CERAMICS
Ceramics is one of the newest material that is used in 3D printing. It is more durable than metal and plastic since it can withstand extreme heat and pressure without even breaking or warping it. Moreover, this type of material is not prone to corrosion like other metals or wear away like plastics do.
This material is generally used in Binder Jetting technology, SLA (Stereolithography) and DLP (Digital Light Processing).
Distinct characteristics:
- It has high-precision components with a smooth and glossy surface.
- It has also resistance to acid, heat and lye.
- It has a wide range of colour
Disadvantages:
- Ceramic requires a great amount of temperature to melt.
- It is not suitable for glazing and kilning processes.
- Since it is fragile, it has limitations in printing objects with enclosed and interlocking parts.
- It is not ideal for the piece assembly process.
ABOUT LATEST AUTOMATIC 3D-PRINTER
Even though 3D printing may be a newly emerging technology, it's rapidly become mainstream in education, manufacturing and lots of other industries. 3D printers allow anyone to simply produce complex parts.
However, these machines have one critical flaw. After a 3D printer has finished printing a neighbourhood, an individual must physically attend the printer and take away the part from the print bed. A 3D printer cannot start its next print job until the previous part is removed. This constraint cripples the productivity of 3D printers. If 3D printers could automatically eject their print jobs, then they might print out a continuing stream of parts. The efficiency of the machine would drastically increase.
Many businesses already use 3D printers to manufacture products. Currently, their manufacturing capabilities are constrained by the necessity to manually remove/start print jobs. If this task was automated, it might be easier for more companies to finish volume manufacturing with 3D printers.
Personally, I add a 3D printing lab that prints many parts for my fellow university students. From my position, it's obvious that this constraint significantly limits the number of print jobs our lab can complete per day.
No comments:
Post a Comment