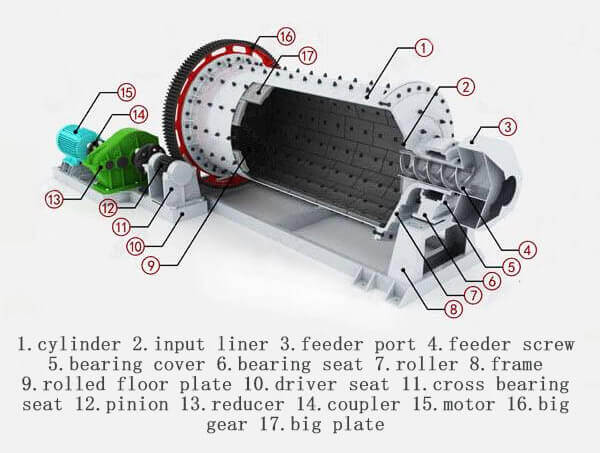
DEFINITION
A pulverizing machine consisting of a rotating drum which contains pebbles or metal balls as the grinding implements. Ball milling may be a simple, fast, cost-effective green technology with enormous potential. one among the foremost interesting applications of this technology within the field of cellulose is that the preparation and therefore the chemical modification of cellulose nanocrystals and nanofibers. Although a variety of studies are reported within the literature, the potential of this system within the field of cellulose nanoparticles has not been fully exploited. This minireview aims at putting existing work into perspective, highlighting the importance and therefore the potential of this green, sustainable technique to facilitate the identification of areas of future development.
ABSTRACT
Ball milling may be a mechanical technique widely wont to grind powders into fine particles and blend materials. Being an environmentally-friendly, cost-effective technique, it's found wide application in the industry everywhere the planet. Since this mini-review mainly focuses on the conditions applied for the preparation and functionalisation of nanocellulose derivatives by ball mill, instead of the machinery itself, the various sorts of machines available in the industry won't be herein described. Nevertheless, a general description of the various sorts of equipment is reported during this section. counting on the appliance, there are different types of ball mill.
However, it generally consists of a hollow cylindrical shell rotating around its axis, which is partially crammed with balls made from e.g. steel, chrome steel, ceramic or rubber. It relies on the energy released from impact and attrition between the balls (grinding or milling medium) and therefore the powder. Advantages of this system include cost-effectiveness, reliability, simple operation, reproducible results thanks to energy and speed control, applicability in wet and dry conditions on a good range of materials (e.g. cellulose, chemicals, fibres, polymers, hydroxyapatite, metal oxides, pigments, catalysts). In contrast, potential disadvantages include the likelihood of contamination, formation of nanomaterials with an irregular shape, noise, long milling and cleaning times. differing types of kit also are available counting on the fabric to be treated, which are described intimately during a recent review by Gorrasi and Sorrentino.19 especially they classify the ball mills in two groups counting on their operation mode: direct and indirect milling. within the first case rollers or mechanical shafts directly act on the particles and transfer the K.E. within the second case the K.E. is firstly transferred to the mill body then to the grinding medium.
These ball mills are the foremost widely utilized in the sector of cellulose and that they are often further divided into three groups: tumbler ball mills, vibratory mills and planetary mills. a glass mill consists of a cylinder partially crammed with steel balls rotating about its longitudinal axis. during this sort of instrument, the efficiency of the method mainly depends on the diameter of the mill. Larger diameters allow the greater height of the autumn and consequently better energy transmitted to the balls. In vibratory mills, the vessel containing the sample and therefore the grinding medium are shaken back and forth at high vibrational frequencies. Important factors, during this case, are the vibrational frequency, the amplitude of vibration and therefore the mass of the milling medium. Finally, during a planetary mill, the vessels are placed on a rotating supporting disk and that they rotate around their own axes. Again, the dimensions of the vessels is an important parameter for the efficiency of the method as a better distance allows a better K.E. and thus stronger impacts.
WORKING PRINCIPLE

It works on the principle of impact and attrition: size reduction is completed by the impact because the balls drop from near the highest of the shell. A ball mill consists of a hollow cylindrical shell rotating about its axis. ... Less wear takes place in rubber lined mills. The length of the mill is approximately adequate to its diameter.
TYPES OF BALL MILLS
1.Horizontal ball mills

The most common sort of product supplied by ball mill manufacturers of India is that the horizontal ball mill. because the name suggests, it comes during a leaner and longer form than vertical ball mills. Though the specifications of their structure and features may vary for each industry, they're basically shaped sort of a cylinder with a drum inside its chamber. The self-same drum is crammed with materials and replenished consequently after every batch. A majority of the horizontal ball mills accompany timers that allow the automated shutdown of the machines upon the entire processing of the fabric.
2.VERTICAL BALL MILLS
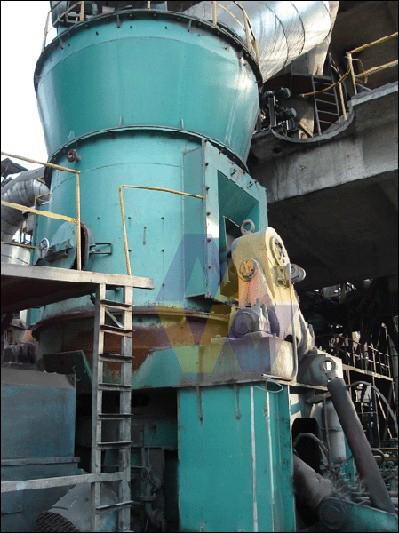
They are specifically designed ball mills that are only manufactured upon request. they are doing not have a detachable drum-like horizontal ball mill and are available within the sort of an erect cylinder. Their processing capacities are limited by their size, making them the not so preferred equipment to be used across industries.

They are intended for usage within the manufacturing factories, where they will process a large number of materials at an equivalent time. Each industrial ball mill has multiple chambers to make sure thorough grinding or mixing of materials. The added materials pass from one chamber to a different to become finely ground and interlinked.

Effects of milling on the properties of cellulose
Ball milling features a high influence on the microscopic and macroscopic properties of the resulting material after treatment, like structure, morphology, crystallinity and thermal stability. The effect of ball mill on the morphological and structural features of cellulose has been described by Okajima and associates.20 They treated microcrystalline cellulose derived from cotton linter during a planetary ball mill at 200 rpm for 4–8 hours in dry and wet conditions with three solvents (water, toluene, 1-butanol). They observed that the various media had an impact on cellulose destruction during the method, resulting in variations in morphology, polymorphism and crystallinity. These differences were attributed to the effect of the solvent on the hydrogen bonding amongst the cellulose particles. In dry conditions, aggregated globular particles (5–10 µm diameter) were formed, with a coffee degree of crystallinity. Globular particles were also obtained in an aqueous medium, but the X-ray diffraction profile showed that the crystalline structure was partly converted to cellulose II and retained some cellulose I crystal. When toluene was used as a solvent, plate-like particles were achieved
A change in morphology of microcrystalline cellulose was also described by Zheng et al., who observed a morphological transformation of microcrystalline cellulose from rod-like to spherical after ball milling was applied. These particles were employed together with starch to supply some pastes, whose rheological properties were remarkably influenced by the concentration of microcrystalline cellulose and therefore the milling time applied to get it.
Further research on the consequences of milling conditions (i.e. ball-to-cellulose mass ratio, milling time, ball size and alkaline pre-treatment) on the morphology of the prepared nanocellulose derivatives was undertaken by the group of Wang. More intimately, they acknowledged that the dimensions of the milling balls have an impression on the formation of fibrous morphologies instead of particulates. Fibre morphology was also considerably influenced by milling time and ball-to cellulose mass ratio.
Interesting studies on the consequences of ball milling on the crystallinity of cellulose were reported by Ago et al., who demonstrated that the mechano-chemical treatment of microcrystalline cotton-derived cellulose within the aqueous environment led to the crystalline transformation of cellulose I into the cellulose II polymorph. Ball milling was performed, during this case, within the presence of 30–50% water in planetary equipment at 400 rpm for two hours. Further studies on the effect of ball milling on the crystallinity and therefore the surface state of cellulose were undertaken by the Saito group, which observed variations of those parameters in aqueous conditions and within the presence of sodium and K-Dur 20 salts. These studies were conducted on microcrystalline cellulose during a tumbling mill machine at 215 rpm for 2–20 hours. The obtained results showed that wet conditions were simpler than dry conditions on the reduction of the degree of crystallinity and therefore the deformation of the sample morphology. Interestingly, the best decrease in crystallinity was observed within the sample containing KCl, whereas the crystallinity of the sample containing NaCl was above when the starting material was milled within the absence of salts. This was explained with the very fact that K+ and Na+ ions acted as water-structure breaker and former agents respectively.
Preparation and chemical modification of cellulose nanoparticles
One of the foremost interesting applications of the ball mill within the field of cellulose is that the preparation of CNCs and CNFs. Being cheap, easy to use and rapid, this method offers several advantages to get nano cellulose and cellulose nanocomposites.28–30 However, the applied conditions (e.g. presence of solvents and catalysts, milling time and speed) got to be carefully monitored to avoid excessive grinding of the raw materials. this system under appropriate conditions and together with chemical or enzymatic treatment also can be used to induce cellulose hydrolysis and depolymerisation. Since the present article mainly focuses on the extraction and functionalization of nano cellulose, these applications won't be discussed, but further information is often found within the literature
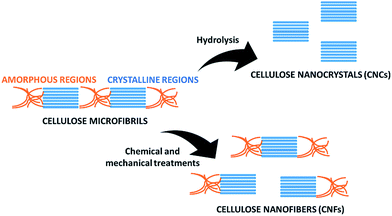
Preparation of cellulose nanocrystals (CNCs)
Cellulose nanocrystals are usually obtained by hydrolysis of native cellulose with mineral acids, which allows the destruction of the amorphous regions of cellulose and therefore the liberation of the crystalline regions (Fig. 3). This process is facilitated by shearing actions. The ball mill allows applying mechanical forces within the presence of chemical agents, therefore it represents a perfect method to mix chemical and mechanical actions to get CNCs. Factors that ought to be taken into consideration are the acid selected for hydrolysis, applied pre-treatments, time and speed of milling, as they will affect the crystallinity, the morphology and therefore the size of the extracted CNCs.
Lu et al. employed the ball mill to get nanocrystals from the bamboo pulp by a mechano-chemical treatment within the presence of orthophosphoric acid.
The pulp was firstly pre-treated employing a Fibre Dissociation Device. The obtained material was then ball milled for 1.5–3.5 hours at 400 rpm within the presence of orthophosphoric acid to offer a transparent solution. during this mechano-chemical approach, orthophosphoric acid worked as a swelling agent during cellulose dissolution and facilitated the disintegration of cellulosic fibres into nanofibers. Double water was then added to separate cellulose from a gelatinous precipitate that was also formed. Cellulose nanocrystals were extracted by multiple centrifugations and a subsequent ultrasonication treatment under stirring for 1–3 hours at 50 °C. The obtained particles were mainly composed of the cellulose type-II polymorph and had a length of 100–200 nm and a width of 13–30 nm. Subsequently, an equivalent research group designed another method to extract cellulose nanocrystals from the bamboo pulp by mechano-chemical activation within the presence of phosphotungstic acid.
Milling was performed for 1.5–2.5 hours, followed by purification and ultrasonication. The resulting nanocrystals had a daily rod-like structure with a curled flat shape, 200–300 nm length and 25–50 nm width. Decisive parameters within the process were the phosphotungstic acid concentration, the response time and therefore the milling duration. especially, at a continuing acid concentration, the yield of the isolated CNCs increased with longer reaction times, with optimal conditions after 4.5–5 hours. The yield also increased by increasing the concentration of phosphotungstic acid from 10 to fifteen. This facilitated the hydrolysis of the amorphous regions of cellulose and therefore the extraction of the nanocrystals. However, at higher concentrations of acid, the yield of CNCs decreased probably thanks to synergistic effects of the acid and therefore the ball milling process on the hydrolysis of the crystalline regions of cellulose.
Conclusion
Ball milling may be a simple, fast, cost-effective green technology with enormous potential. The studies reviewed showed its applicability to organize and chemically functionalise cellulose nanocrystals and nanofibers. one among the most advantages of this method is that the possibility to mix it with chemical treatments, thus allowing obtaining the specified products with minimal effort. Nevertheless, variety of things has got to be taken into consideration, which may affect the features of the isolated nanocelluloses (e.g. milling time, speed, sort of solvent, pre-treatments). Optimisation of the tactic is therefore of fundamental importance to isolate CNCs and CNFs with the specified properties. Features which will be affected include crystallinity, thermal degradation, length, width and morphology of the isolated nanoparticles. However, it shouldn't be forgotten that the source of the raw starting material also can have a substantial impact on the efficiency of the tactic and thus the properties of the extracted nanocelluloses and therefore it should be carefully selected.
Although ball milling technology has been exploited in process engineering, organic synthesis and therefore the formation of nanocomposites, its potential to isolate and chemically modify cellulose nanoparticles has not been fully explored, as only a limited number of studies has been administered . especially , further studies on the functionalisation of CNCs and CNFs would be of great interest, because it is usually problematic to react these materials, thanks to their low solubility in water and organic solvents. To our knowledge, esterification is that the most ordinarily reported reaction; however, other sorts of chemical modification might be explored, although limited by the functional groups present. Options, for instance , might be other reactions where the cellulosic hydroxyl groups act as a nucleophile.
Moreover, since ball milling are often employed in dry and aqueous conditions, it could represent a green, sustainable technology for industrial application. Further studies on the preparation of cellulose-based nanocomposites would even be of interest as this system offers an easy , fast thanks to obtain such hybrid systems.Since this is often a promising technology, we hope that this minireview will help to know its significance and potential and can facilitate the identification of areas of future development.
No comments:
Post a Comment